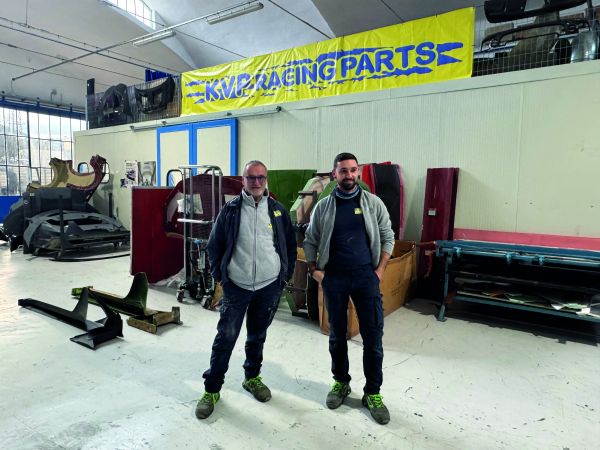
Siamo stati a Busalla, in provincia di Genova, quartier generale di una realtà che dal 1986 si occupa di produrre pezzi speciali in vetroresina e carbonio: KVP
Nata per la volontà e la passione di 3 soci e fratelli sulle ceneri di una carrozzeria, KVP Vetroresine comincia con la produzione di pezzi in fibra di vetro per auto da corsa, materiale che dal 1982 comincia ad essere utilizzato nel settore racing per la realizzazione di pannelli di carrozzeria e appendici aerodinamiche, dato il peso ridotto del materiale rispetto all’acciaio. Nel settore dei componenti di carrozzeria alleggeriti, soprattutto per fuoristrada da competizione, KVP inizia l’attività con la realizzazione di parti in materiale composito in kevlar e fibra di carbonio. Prosegue con produzioni molto più importanti e seriali quali la scocca della prima vettura ciclomotore Casalini Ydea, che si poteva condurre senza targa e patente. Negli anni la produzione di KVP si amplia e comincia a spaziare anche nel settore dei veicoli pesanti, con la costruzione di cabine di mezzi spalaneve per esempio, e nel settore nautico, con la realizzazione di moltissimi particolari presenti a bordo di navi da crociera e traghetti. Il cuore, però, batte sempre per l’automotive, il settore da cui tutto è partito e che, negli anni, ha portato KVP a essere un riferimento per la produzione di manufatti in materiale composito. «Nel 1983 abbiamo cominciato a produrre le scocche dei sedili da corsa di OMP, sia in resina che in carbonio, e le slitte delle Delta da rally».
DIVERSIFICARE la PRODUZIONE
«Nel frattempo – continua Carlo Pardi – abbiamo cominciato a produrre pezzi anche per altri settori per diversificare la produzione». Come accennato, però, testa e cuore sono sempre rivolti verso le auto e mai KVP ha abbandonato la produzione di componenti di carrozzeria; nel 2023 è stata rilevata una storica realtà che produceva esclusivamente per il settore auto continuando ed ampliando, di fatto, il proprio business di partenza e acquisendo nuovi clienti: KVP rientra a pieno titolo nella produzione di pannelli e ricambi per auto, in particolare del mondo racing e vintage. Il portfolio di articoli in archivio e a catalogo è di tutto rispetto e comprende componenti di moltissime auto fra le quali Ferrari F40, Lamborghini Huracan, Lancia Delta Integrale e molte altre supercar. Abbiamo voluto fare visita anche alla linea di produzione dei pezzi in carbonio, un vero e proprio laboratorio dove il fattore umano è ancora fondamentale. Si parte dalla scelta del materiale in base al tipo di ricambio da produrre, al suo utilizzo o alla finitura voluta dal cliente. Ci sono bobine di fibra di carbonio e kevlar ovunque, con trame e finiture differenti; una volta scelta quella corretta, il foglio “nudo e crudo” viene steso su un secondo strato, che altro non è che un film di resina con dell’impregnante. L’assemblato viene poi tagliato, a mano con le forbici se il particolare non è grosso o a laser se il ricambio ha forme e dimensioni particolari. Al foglio ora va data una forma e quindi viene steso su stampi che ne vanno a riprodurre le forme in 3D; una volta terminata questa fase di costruzione e assemblaggio si procede a insacchettare il grezzo del ricambio, avvolgendolo in un sacco per il vuoto e portando il tutto a una pressione negativa di 0,9 bar. Messo tutto sottovuoto si può procedere alla cottura dei pezzi e ciò avviene in 3 step: una prima fase che dura 1,5 ore a 70 gradi, una seconda cottura di un’ora a 90 gradi e lo step finale di mezz’ora a 130 gradi. «Dopo che i pezzi sono usciti dal forno vanno lasciati raffreddare e poi si può passare al controllo qualità e alla finitura. Il vantaggio del carbonio o del kevlar è l’eccezionale resistenza con ingombri e pesi molto ridotti», chiude Carlo Pardi, pronto a passare il testimone al figlio in azienda da ormai più di 10 anni, nel segno della continuità familiare.
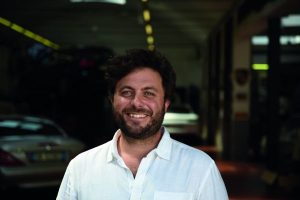
Federico Lanfranchi
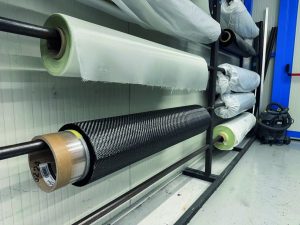
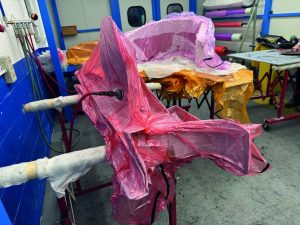
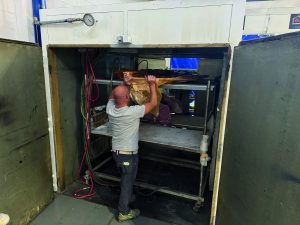
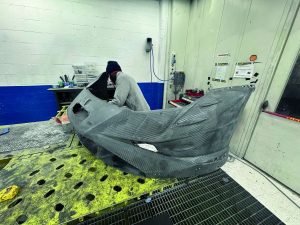
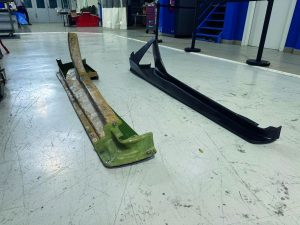
a cura di Federico Lanfranchi
Condividi l'articolo
Scegli su quale Social Network vuoi condividere