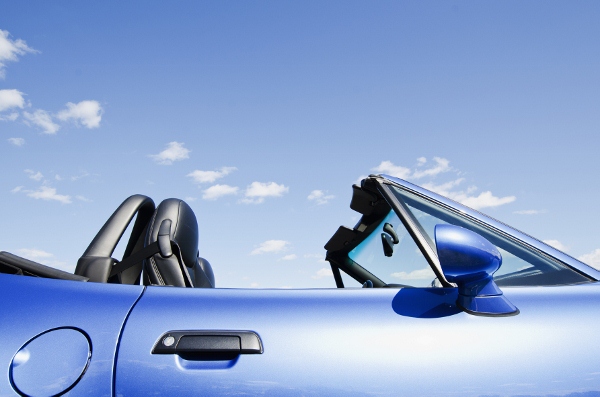
Axalta analizza come le nuove carrozzerie multi-strato leggere e le vernici con essiccazione a basse temperature stiano guidando l’innovazione e rappresentino una sfida per il settore
Guidato da una forte spinta verso la sostenibilità, il design delle carrozzerie dei veicoli sta radicalmente cambiando. Axalta Coating Systems si è messa al lavoro per affrontare le sfide che questi nuovi materiali leggeri presentano.
Spinta verso l’evoluzione
Gli enti regolatori stanno mettendo una sempre maggiore pressione sull’industria dell’auto per un utilizzo di materiali e processi più sostenibili. Negli ultimi decenni le varie norme volte alla riduzione delle emissioni di VOC e di CO2 e ad una maggiore efficienza dei carburanti hanno portato il settore delle vernici a sviluppare nuovi prodotti eco-sostenibili come i materiali Alto Solido, i materiali all’acqua, i sistemi che non richiedono l’utilizzo di primer e i sistemi 2-wet o 3-wet. Allo scopo di ridurre il peso totale della carrozzeria dei veicoli, gli OEM sono intenzionati a fare un uso sempre maggiore di materiali leggeri come alluminio e magnesio e substrati polimerici. I processi e i materiali di verniciatura dovranno anch’essi essere adattati. Nel caso dei substrati polimerici, per esempio, si devono diminuire le temperature di essiccazione.
Le implicazioni di una carrozzeria leggera
I materiali leggeri aiutano a tagliare le emissioni di CO2 nell’ambito delle carrozzerie in quanto è possibile ridurre il consumo energetico utilizzando vernici con essiccazione a bassa temperatura. Grazie alle opportunità legate alla geometria dei veicoli, questi materiali leggeri offrono anche una più ampia scelta stilistica. Le scelte di verniciatura della carrozzeria e delle parti in plastica legate al tipo di produzione si traducono anche nella possibilità di migliorare l’armonia del colore e di semplificare il ciclo degli approvvigionamenti. Questi substrati leggeri rappresentano però comunque una sfida per il settore delle vernici: dovranno per esempio essere sviluppati nuovi processi in grado di avere un impatto sull’essiccazione di adesivi e vernici. Si dovrà anche assicurare la durabilità sul lungo termine e la riverniciabilità con essiccazione a bassa temperatura oltre che l’armonizzazione della finitura finale su vari e diversi substrati.
Tecnologie di vernici esistenti e possibili per sistemi con essiccazione a bassa temperatura
Esistono già alcune soluzioni di vernici con essiccazione a bassa temperatura, come per esempio i processi usati per le parti in plastica delle auto, per camion che richiedono un’immagine sempre più curata e una qualità sempre maggiore da primer e smalti con essiccazione a basse temperature e da OEM specializzati i cui tintometri per i prodotti con essiccazione a basse temperature forniscono piccole quantità di tinte particolari per clienti specifici.
Le nuove soluzioni e processi devono comunque affrontare le sfide poste dai mix di substrati di più recente creazione.
Tutte le tecnologie di vernici adatte a sistemi con essiccazione a basse temperature presentano dei vantaggi e degli svantaggi. Con sistemi che possono sostenere un’asciugatura a raggi UV, la finestra di essiccazione può essere abbassata a temperatura ambiente ma ci possono essere dei problemi per le zone dove i raggi non arrivano. Questi problemi possono essere evitati montando le lampade UV su robot capaci di raggiungere tutte le aree interessate. Questa soluzione potrebbe essere usata in abbinamento con un sistema all’acqua 3-wet o senza primer ed offrirebbe la possibilità di ridurre i tempi totali di essiccazione sino al 70%.
Altre tecnologie di reticolazione, come l’Acido Epossidico 2K, Acrilico/Melammina 2K con catalizzatore non bloccato o Acrilico/Melammina 1K con catalizzatore bloccato, possono ridurre i tempi di essiccazione ma potrebbero presentare altri problemi relativi a stabilità o proprietà tecnologiche. Per adesso la migliore tecnologia di reticolazione per vernici con essiccazione a basse temperatura sono i poliuretani 2K.
Un’altra opzione è rappresentata dai (poli) aspartati che sono accessibili attraverso una semplice procedura di sintesi. Questa opzione sembra poter avere buoni risultati rispetto alle proprietà tecnologiche come durabilità e resistenza agli agenti chimici persino con un’essiccazione a temperatura ambiente grazie a una reticolazione estremamente veloce. Ciò offre anche la possibilità di formulare vernici a più alto contenuto di solidi allo scopo di abbinare i benefici di un’essiccazione a basse temperature con una minore emissione di solventi.
Esiste anche un’altra, e non meno importante, sfida rappresentata dalla possibilità di abbassare i tempi di essiccazione per le vernici per elettrodeposizione perché nel futuro design delle carrozzerie auto i componenti metallici saranno sempre più presenti. Il percorso che porta a vernici per elettrodeposizione con essiccazione a basse temperature può essere suddiviso in tre fasi di sviluppo. La prima è un obiettivo di temperatura massima di 180oC sulle parti esterne che significa temperature minime di 165oC -170oC. Ciò potrebbe contribuire alla riduzione dei consumi energetici all’interno delle carrozzerie. Axalta ha avuto dei risultati positivi grazie alla tecnologia Aqua EC4027 attualmente commercializzata con la quale in 10 minuti a 150oC è stata raggiunta una buona resistenza ai solventi e alla corrosione.
La prossima fase dello sviluppo potrebbe portare a temperature che permettono la verniciatura di parti in plastica specifiche (Temperatura massima = 140°C), in altre parole le parti in metallo e in plastica possono essere immesse nella vasca per elettrodeposizione e smaltati durante la produzione. In questo caso vi sarà bisogno di un nuovo processo di reticolazione e di un significativo sviluppo dei processi e dei materiali. La questione delle temperature più alte necessarie per l’acciaio dovrà anch’essa essere affrontata.
I potenziali benefici di un’ulteriore riduzione delle temperature per i prodotti per elettrodeposizione sino a per esempio 80oC -125oC devono ancora essere verificati. Si tratta comunque di un processo di sviluppo sul lungo termine.
Le carrozzerie leggere porteranno inevitabilmente ad ulteriori innovazioni nei campi dell’essiccazione a basse temperature, dei materiali e dei processi. E mentre alcune tecnologie sono già disponibili, si sta lavorando ad alcuni nuovi sviluppi in grado di rispondere alle sfide poste dai nuovi materiali. Il prossimo passo dovrà essere una maggiore integrazione delle singole soluzioni – materiali, processi e applicazione – in ambienti di produzione di massa.
Condividi l'articolo
Scegli su quale Social Network vuoi condividere